10 Best Multi Mill Manufacturers & Suppliers in India
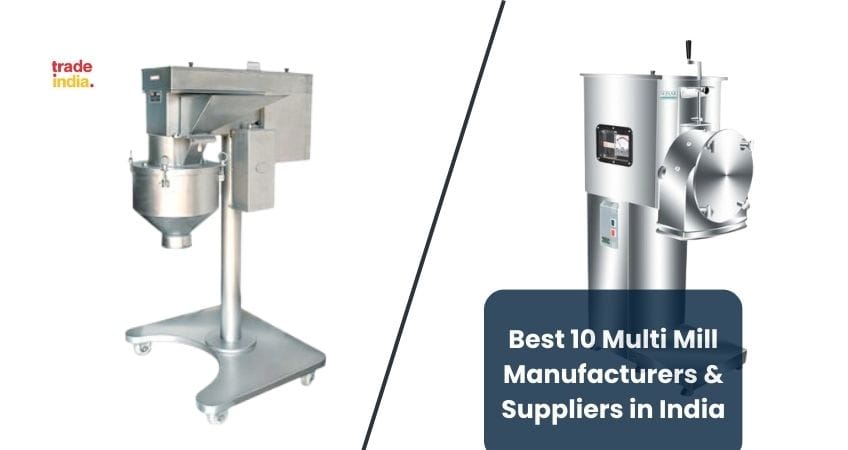
Innovation is the primary driver of advancement in the realm of industrial production. The multi-mill is one such innovation that has made waves in a variety of industries. A multi-mill, as the name implies, is a flexible piece of machinery designed to accomplish various duties during the production process. This blog delves into the fascinating realm of multi-mills, investigating its features, uses, and influence on current industrial practises.
Consider a single machine that can execute a variety of jobs that would normally need many devices. Multi-mills exemplify this notion by merging many functions into a single compact device. These powerful machines can handle everything from milling and drilling to cutting and shaping. Their interchangeable tooling systems, which allow operators to quickly switch between functions, are at the basis of their adaptability.
Features that Set Multi-Mills Apart
Interchangeable Tool Heads: Multi-mills include quick-change tool heads, which let operators to go from one operation to another without spending time on lengthy preparations. This adaptability leads to more productivity and less downtime.
Computer Numerical Control (CNC) Integration: CNC technology is used in many current multi-mills, allowing for precise control over motions and processes. This level of automation maintains consistency and lowers the possibility of human mistake.
Computer Numerical Control (CNC) Integration: CNC technology is used in many current multi-mills, allowing for precise control over motions and processes. This level of automation maintains consistency and lowers the possibility of human mistake.
Enhanced Precision: By combining sophisticated technologies like as CNC and high-precision sensors, multi mill machine can produce complicated designs and tight tolerances with astonishing accuracy.
Applications Across Industries
automobile Manufacturing: Multi-mills are widely used in the automobile sector, where precision and efficiency are critical. These robots streamline production processes by fabricating delicate engine components and producing moulds for body panels.
Aerospace Sector: Because of the crucial nature of its components, the aircraft sector requires parts with flawless precision. Multi-mills are essential in the production of complicated elements such as turbine blades and structural components.
Production of tooling and dies necessitates a mix of cutting, shaping, and finishing operations. Multi-mills thrive in this category because they enable producers to accomplish all of these activities on a single machine.
Medical Device Manufacturing: Multi-mills help to manufacture complicated medical devices and implants. Their versatility with a wide range of materials, including metals and polymers, makes them vital in this industry.
The Impact on Manufacturing Practices
Reduced Capital Investment: Multi-mills help producers save money on equipment by reducing the requirement for many specialised machines. This has the potential to be a game changer, particularly for small and medium-sized businesses.
Faster Turnaround Times: Because of the smooth transitions between functions, manufacturing cycles are shorter. Manufacturers can adapt to market demands faster and cut lead times.
Optimised labour utilisation: When compared to a multi-machine arrangement, multi-mills require fewer operators. Skilled employees may manage a single multi-mill operation, freeing up human resources for other duties.
Improved Quality Control: Multi-mills contribute to consistent quality across batches through automated procedures and CNC accuracy. This is critical in businesses where even tiny variations can have disastrous implications.
The multi-mill emerges as a beacon of efficiency, variety, and development in the changing world of industrial manufacture. Its capacity to execute a variety of activities on a single machine is changing the way producers think about manufacturing. As technology advances, we should expect increasingly more complex multi-mill designs that push the frontiers of what is feasible in the production sector. The multi-mill revolution has here, and its influence will be felt across sectors for many years to come.
10 Best Multi Mill Manufacturers & Suppliers in India
India has a booming industrial sector, and some businesses stand out in multi-mill production for their quality, creativity, and commitment to the area. The following are 10 best multi-mill manufacturers and suppliers in India:
Cadmach Machinery Co. Pvt. Ltd.:
Known for its innovative pharmaceutical machinery, it builds multi-mills for a variety of industries, assuring precision, efficiency, and compliance with international standards.
Prism Pharma Machinery:
It focuses on the pharmaceutical, chemical, and cosmetic sectors for offering multi-mills with sophisticated features like as GMP compliance and user-friendly controls.
Fluidpack:
It specialises in pharmaceutical packaging and processing gear, such as multi-mills intended for efficient size reduction and consistent material mixing.
SaintyCo:
A global provider of pharmaceutical equipment, including multi-mills, designed to improve manufacturing processes and satisfy regulatory criteria.
Saimach Pharma:
It provides adaptable multi-mill solutions for the pharmaceutical, chemical, and cosmetic industries, with an emphasis on precision, sanitation, and convenience of use.
Nu Pharma Engineers & Consultant:
This firm provides multi-mills for the pharmaceutical industry, with a focus on characteristics like as rapid changeover, safety, and little maintenance.
GMP Equipments Pvt. Ltd.:
A pharmaceutical equipment manufacturer, it develops multi-mills that allow for efficient and controlled processing while adhering to high quality requirements.
Shakti Pharmatech Pvt. Ltd.:
It manufactures multi-mills and other pharmaceutical gear to improve manufacturing processes and assure consistent quality.
Kothari Pharma Technologies Pvt. Ltd.:
With a broad variety of pharmaceutical machinery, it provides multi-mills that meet the increasing demands of the industry.
Mittal Engineering Works:
Known for its pharmaceutical and chemical equipment, it manufactures multi-mills that are precise and versatile, assisting industries in producing high-quality output.
When evaluating multi-mill manufacturers and suppliers in India, consider criteria such as product quality, technical innovation, customer reviews, and compliance with industry standards. Through their cutting-edge multi-mill solutions, these enterprises contribute to the growth and development of numerous industries in India.
FAQ's: Multi mill
Q. What is a multi mill and what are its main functions?
Ans. A multi mill is a flexible industrial equipment used for size reduction and material processing operations in a number of sectors such as pharmaceuticals, chemicals, food processing, cosmetics, and others. It is intended to execute numerous operations inside a single unit, reducing the need for separate machines and increasing industrial efficiency.
The main functions of multi-mill:
Size Reduction: Reducing the size of materials is one of the key purposes of a multi mill. It does this through the use of cutting edges, revolving blades, and a screen. A hopper feeds the material into the machine, and revolving blades or beaters break it down into smaller particles. These particles are then screened to attain the appropriate particle size.
Mixing and blending: Multi mills include blades or beaters that allow for effective mixing and blending of various ingredients. This function is especially significant in sectors such as pharmaceuticals and food processing, where constant and uniform mixing is critical for ultimate product quality.
Homogenization: It is the process of breaking down bigger particles into smaller, homogenous particles in order to guarantee an equitable distribution of components. By processing materials through their cutting and mixing operations, multi mills can accomplish homogeneity.
Granulation: The process of creating bigger granules or aggregates from smaller particles is known as granulation. Multi mills can be used to granulate materials, such as those used in the pharmaceutical sector to manufacture tablets or capsules.
Pulverisation is the process of converting solid materials to a fine powder. Multi mills can effectively pulverise a variety of materials, including spices, herbs, and medicinal compounds, by breaking them down into small particles.
Multi mills can be used for shredding or decreasing the size of huge things into smaller, manageable bits in specific situations. This is a term that is frequently used in recycling procedures.
Screening: Screens in multi mills enable for controlled particle size reduction. Screens may be simply adjusted to achieve varied particle sizes based on the process's individual requirements.
Q. How does a multi mill work in pharmaceutical and other industries?
Ans. A multi mill is a multipurpose equipment that may be used in a variety of sectors such as medicines, chemicals, food processing, and cosmetics. Its operating premise is constant throughout different industries, with occasional changes depending on individual needs. Let us look at how a multi mill works in the pharmaceutical and other industries:
- Material Intake and Feeding
- Size Reduction and Processing
- Screening and Sizing
- Collection and Discharge
Multi mills are a cost-effective, efficient, and adaptable solution for a variety of processing demands in all of these sectors. They are critical in optimising production processes, enhancing product quality, and adhering to industry requirements.
Q. What are the key features to consider when selecting a multi mill?
Ans. To achieve optimum performance, efficiency, and safety, it's important to carefully evaluate a variety of aspects when choosing the best multi mill for your particular application. When choosing a multi mill, bear the following important characteristics in mind:
- Type of Material and Application
- Capacity and Throughput
- Size of Particles
- Material of Construction
- Ease of Cleaning and Maintenance
- GMP Compliance
- Safety Features
- Customization and Adaptability
Q. Can the multi mill be customized to meet specific requirements or industry standards?
Ans. Yes, multi mills can often be customized to meet specific requirements or industry standards. Manufacturers understand that different industries and applications have unique needs, and they may offer options for customization to ensure that the multi mill aligns perfectly with those requirements.
EXPLORE MORE: