Top 10 Benefits of Mezzanine Flooring - 2023
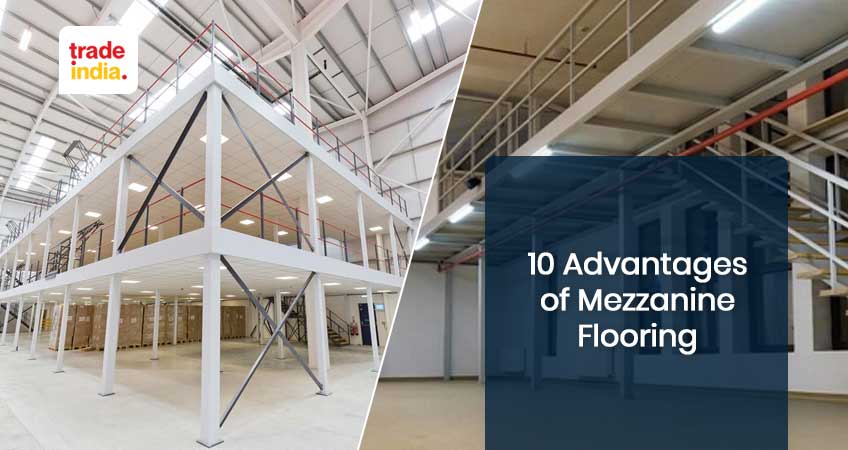
According to Section 505 of the International Building Code, a mezzanine is any level or levels located between the ground floor and the uppermost story. The word "mezzanine" comes from the Italian word "mezza," which signifies "half" or "middle."
A mezzanine level is a great way to make the most of a building's square footage. Mezzanine levels can range in size from a huge structural steel mezzanine system to a long equipment or work platform or even a small storage platform. Equipment platforms are not the same thing as mezzanines. When it comes to construction and building codes, knowing the difference between a mezzanine and an equipment platform is crucial.
Many materials, including steel, wood, and concrete, are used in the construction of mezzanines. The majority of industrial mezzanine floor are constructed from high-strength steel enabling simple installation within existing buildings.
Top 10 Benefits of Mezzanine Flooring
1. Inconspicuous Design
The beautiful thing about mezzanine levels is that they simply permit designers to tailor their solutions to the specific needs of any individual organization. For instance, the suspended ceiling space can be utilized for the installation of power and data cables. Data points can be placed anywhere on the mezzanine, giving you more options for how to arrange your office space.
There is also the option of running power cables along the columns of the mezzanine, which would provide convenient access to electricity for any machines or workers located below the mezzanine. Also, the column grid will be created according to your desired specifications for the space below the mezzanine. Optimizing the column grid design can cut costs and construction time in half by using less steel.
You shouldn't include columns in your manufacturing mezzanine floor design unless they're absolutely necessary. If you want to make the most of the space you have, you should aim for the most minimalistic design feasible. Mezzanine columns can be concealed in the wall or built into the design of your shelves to make this possible.
2. Enhances space use
A mezzanine level is a great way to take advantage of the spare space that you currently own and put it to productive use. Because of the high cost of renting or buying new warehouse space, it makes sense for rapidly expanding companies, like online mezzanine floor manufacturers, to build up instead of out. Well-built mezzanines can double the amount of usable space below it.
3. Easily handles weight
Mezzanine flooring in factories can be reinforced to support enormous weight. A mezzanine floor built for an office is typically constructed to support 360kg per square meter, while a mezzanine floor built for storage or production can support up to 500kg per square meter.
Mezzanine floors, on the other hand, can be built to support as much as one ton per square meter, making them perfect for factories and other industrial settings with heavy equipment. Nevertheless, you'll likely need to modify the slab's base in order to do so.
The warehouse slab details can be found in the operations and maintenance document that was handed to you when the facility was constructed, and they will tell you how sturdy your current concrete floor is. Ask your landlord for this data if you're a lessee.
If you can't locate this info, your mezzanine floor contractor should be able to assist you in arranging a core test sample to be taken.
4. Versatile & Bespoke
Makers innovative Revlok modular mezzanine system is just one example of how this type of design may create a multipurpose area. Your industrial mezzanine floor design can be customized to include everything from additional office space and break spaces to packing zones and overflow racking.
5. Cost Effective
Earlier, we discussed how adding a mezzanine floor is more cost-efficient than relocating to a new location. Nonetheless, they are less expensive than alternatives like a block and beam structure for making new room. In terms of cost per square foot, mezzanines are typically more affordable, and they also offer greater architectural freedom.
Instead of transferring to a new building, you may take use of the extra space by adding more employees by installing a mezzanine floor option within your current factory.
When relocating, a mezzanine floor solution within your new factory may also allow you to select a smaller location than you had originally anticipated. The resulting decrease in rent and rates will take effect immediately.
It is possible to increase the amount of usable space in a building by a factor of two or three just by shifting one's focus from the 2D footprint to the 3D area above ground.
6. Future Planning
Your business plan will include projections for the company's future expansion. Whether or not you have immediate need for additional space, planning ahead to create a mezzanine floor could help you avoid having to deal with an invasive installation in the future.
Given that mezzanine floors may be tailored to meet the changing needs of a company, they are increasingly popular with expanding firms. You, as a business owner, will have anticipated expansion opportunities as your revenue rises.
It could be new machinery to increase output, or it could be more space in the office to support staff growth. An industrial mezzanine floor level can be installed quickly and at cheap expense, making it possible to prepare for such contingencies.
A mezzanine floor, for instance, can be constructed within your building as the bare steel framework for an office, storage, or production area. This makes it simple for the mezzanine floor contractor you hire to come back at a later date and put in the chipboard as part of the overall solution you want.
7. Dismountable and Re-locatable
Your mezzanine level can be easily disassembled and moved to a new location if your company outgrows its current quarters. Modular solutions, such as a mezzanine floor system, make it simple to relocate an existing mezzanine to a new warehouse with a completely different layout.
Cold-rolled steel sections are used in the production of mezzanine floors because they are lighter and more manageable than the conventional rolled steel joists.
8. Quick & Easy Installation
Mezzanine installation is more quicker than other warehouse expansion choices due to the ease of design & simple yet effective design. When compared to conventional building methods, the modular mezzanine system can cut installation time for mezzanines by as much as half.
9. Minimizes downtime during Construction
The process of installing a mezzanine level in an otherwise vacant warehouse is quite simple. It is not necessary to take into account the needs of your staff in order to minimize downtime. It's a different story, though, if you're expanding your plant within its already-existing footprint.
Yet, you shouldn't be concerned because any competent mezzanine floor specialist will take all precaution to limit the impact on your business as usual. They can design the mezzanine structure to fit your existing equipment or production line layout, and they can construct it at any time of day or night.
You won't even have to relocate your big machines very often. The mezzanine floor in house contractor you hire should safeguard them throughout construction. They'll also coordinate delivery times to avoid interfering with your workday.
The current on-site staff will be given an introduction to the construction site and informed on the ongoing progress. Safe walkways will be built, and all work areas will be gated off and labeled with signs warning of potential hazards and outlining recommended practices.
10. Eases Congestion
The nature of a successful business necessitates the presence of high foot traffic locations. But, there are instances when a separate, quieter area is clearly required. This need can be met with the help of a mezzanine, which provides a raised platform away from potentially dangerous forklifts and other heavy machinery. By allowing workers more room to move around, you can lessen the likelihood of accidents and boost their efficiency at work.
Comparison of Mezzanine Flooring Manufacturers in India: Price Range, Rating
As you can see, there are numerous gains to be made by adding a mezzanine level to your manufacturing facility. Both in terms of cost and adaptability, they are an excellent choice. There is a mezzanine floor option that can work for your company.
The mezzanine floor designers have worked with enterprises of varying sizes and scopes to provide custom mezzanine floor solutions. They can assist you in finding warehouse space for your items or office space for your expanding staff.
FAQs: Mezzanine Flooring
Q. What materials are used to build Mezzanine Floors?
Standard materials for mezzanine flooring include stainless steel, steel, wood, , concrete, and even fiberglass. The materials used to build a mezzanine level must take into account the mezzanine's intended function. Most mezzanines are built using steel and concrete.
Q. What is the maximum height of a Mezzanine Floor?
The mezzanine level must be large enough for even the tallest people, and the area below the mezzanine must be functional as well. Having a mezzanine with a fully functional area below it requires a ceiling height of at least 14 feet (4.2m).
Q. What kind of businesses typically use Mezzanine Floors?
Manufacturing facilities, distribution hubs, warehouses, and repairing sectors can use Mezzanine floor space for storing or completing task.
Q. How much does it cost to install a Mezzanine Floor?
The cost to install a Mezzanine floor is Rs 230/square feet.
Related Blog Topics:
Tips to Start A Floor Cleaning Business
Top 10 Tile Manufacturers, Suppliers & Exporters in India