How To Start Digital Thermometer Business?
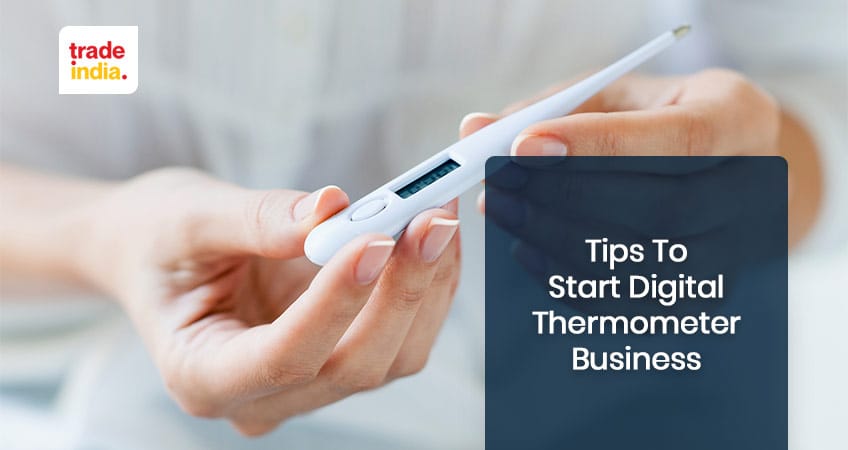
India has come a long way when it comes to perfecting its practices in the medical field. Deep-rooted in its history and culture were traditional methods and remedies that dominated patient care systems in India, but tides are turning, and India is steadfastly adapting to more digital and technologically dependent ways to revamp its healthcare system.
The Covid-19 pandemic has set out an alarm and cemented people’s belief in the saying that “Prevention is better than Cure”. Wherever you go nowadays, you will find your temperature taken with infrared thermometers considering recent incidents as a step towards precaution and more than ever, Digital thermometer sales soared during recent times, with supply failing to match up with the pent-upped demand.
The market for Digital thermometers is expected to reach around $1.5 billion by 2025, with demands to keep on surging with time. You may think that venturing into this industry provides a lucrative option but there are a lot of factors that need to be considered and take advantage of this business opportunity.
Step 1: Understand the Market and the Product
The market potential for digital thermometers has been growing as their demand has been high in the healthcare, medical, domestic, and hospitality sectors due to the increasing transmission of illnesses, flu, and viruses, to maintain a sanitary and safe work environment.
The use of thermometer include:
- For routine check-ups among the household's elder and newborn population.
- To be utilized in hospitals, clinics, medical laboratories etc
- To check the temperature of the external environment.
- To prevent food and beverage contamination and deterioration in the F&B industry
- Offices and manufacturing facilities will utilize it to provide a safe working environment.
If we are to categorize them based on Type, they can be broadly placed as:
Step 2: Understanding the Target Customers
Healthcare:
Hospitals, clinics, and other healthcare institutions require digital thermometers to check on their patients' temperatures before making a diagnosis.
Manufacturing:
Manufacturing environments, such as factories, warehouses, and storage, require digital thermometers for frequent checks of workers, labours, and other personnel to provide a healthy working environment.
Laboratories:
For the aim of monitoring the temperature of their samples, they require digital thermometers.
Automotive Industry:
Infrared digital thermometers are used to monitor car heating and ventilation systems to ensure that they comply with regulatory requirements.
Restaurants and Catering:
Digital thermometers are used in restaurants, catering, and cooking to guarantee that food is cooked through, to monitor the temperature of boiling oil, and ensure that the dish is done.
Airports:
These digital thermometers are used only by airports to monitor the temperature of passengers and cabin staff on board due to worries about oxygen levels.
Commercial Establishments:
Commercial areas, such as workplaces, institutions, and other commercial spaces, require digital thermometers to protect the health of their employees and staff through regulatory health checks.
Greenhouses and horticulture:
Digital thermometers are used to monitor the air temperature and moisture level to continue with the cultivation and plantation activities.
Read More: How to Start an Allopathic Medicine Wholesale Business?
Step 3: Build a Strategy
Before entering the field, you must be aware of the business environment, market structure, and your competitors to better market and position your product. You must identify the target customer group from the categorization we did previously, then you have to understand the competitors who are already in the field, the thermometer price that they are getting for their product and the strategies they are adopting to market the products. After you have analyzed these things, you will find the exact place where your product will become successful.
Step 4: Production and Logistics
After you have laid down your strategy, you will get an estimate of your target group of consumers and the amount of product they may need annually. Based on these, you must set up your manufacturing plant and allocate capacity. Thermometer manufacturers also need to take into consideration the channel of distribution for their products, the number of middle players they want to involve and the location they will be serving. It is better to allow for a lean manufacturing system to increase productivity and profitability.
Step 5: Marketing
Now that you have planned out your business process, it is time to show your consumers what you are giving them and what price you will be asking from them. Though the number of players in this field may be limited, thermometer price, unique stand-out features, competence, reliability, and accuracy are some of the parameters that one should look to achieve differentiation in.
What are the requirements for the manufacturing of digital thermometers?
Area
Based on the industry average, an allocation of 300-500 sqft area is optimal for setting up a business unit. However, it will vary depending on the production level that you want to achieve.
Raw Materials
Raw Materials used for the manufacturing of digital thermometers can be sourced from local suppliers as well as international players. Price competition makes it necessary to source from international suppliers few raw materials, but these prices are highly volatile and based on government trade regulations. The raw materials needed for manufacturing would include Glass, Black Ink, Scale, Spirit-Filled Liquid, Wax Solution, Packing Materials etc. Based on the type of thermometer you are manufacturing; this is like to change.
Machinery
Your manufacturing and production unit will be efficient when machinery and equipment are maintained and handled well. Since this is a very delicate industry, special care is needed for Quality control. The machinery needed would include a Glass Tube making machine, a Bulb Reservoir machine, Mercury/Hydrocarbon fluid dispenser, a Temperature controller and a Packaging Machine.
Manpower
A rough estimate places the manpower needed at 10 for an initial factory set-up. 4 skilled, 3 unskilled and 3 management level employees will be needed to maintain the workflow. The manpower needs to be increased based on demand and training needs to be provided on equipment handling.
Setting up in India
Learn About Competitors
There are a lot of thermometers manufacturers in India. It is important to understand the business model they use to operate and the customer segment they serve. Sometimes partnering up with an existing player in the field like some digital thermometer manufacturers or digital thermometer dealers in India opens more opportunities and leverages the network laid out by them. This will also help you understand the different suppliers, the government regulations and help keep you up to date with industry changes.
Some of the thermometer manufacturers in India are:
- Hicks Thermometers India Ltd.
- Indosurgicals Pvt Ltd
- RAJ Thermometers
- Calcutta Instrument Corporation
- Jindal Medical & Scientific Instruments
Some of the top digital thermometers dealers in India are:
- Hemant Surgical Industries Limited
- Kannu Impex Private Limited
- Elegance Asia
- Sarvam Supplies
- Korrida Medical Systems
Consumer Identification and Marketing
It is not necessary that you have to become a B2C player in the field. It is perfectly safe for a B2B player but depending on the customer segment that you are serving, you must revise your marketing strategy. Mass Media channels may not be suitable when you are a B2B player. Similarly, when you are a B2C player, promoting aspects such as features, thermometer price, longevity, and reliability on platforms such as Television, Radio, and social media can go a long way to ward off competition.
Regulations
The Government of India has several restrictions and licenses that are needed in order for a player to enter this field. One should pay attention to these rules from time to time as they keep on changing based on advancements in the field. Some of the major licences that would be required would include:
- BIS Certificate
- ISI Mark
- Certificate of DCGI
- Trade License
- MSME Registration
- GST Registration
Conclusion
There is a rising demand in the field for digital thermometers and the need for a routine check-ups has increased the customer pool immensely. As more players realise the need for sanitation and a healthy lifestyle, the demand for the same is set to rise more. The set-up of the plant and business may involve a lengthy process as you are entering into an industry that is highly concentrated and delicate to operate in given the end consumers but the profitability estimates for the industry makes it worthy enough to venture into this space with a set business plan and model backing you up.
FAQs: Digital Thermometers
Q. What is the rough capital that would be needed to set up the unit?
Ans: An initial investment of around 10-15 lakhs would be needed to set up the business which would involve around 70% of costs going to fixed investments and the rest 30% as working capital requirements.
Q. Which machines are needed for manufacturing and production unit of digital thermometer?
Ans: Glass Tube making machine, Mercury/Hydrocarbon fluid dispenser, a Bulb Reservoir machine, a Temperature setter and a Packaging Machine are required for manufacturing and production unit of digital thermometer.
Explore More :