Why The World Is Demanding More Cobalt?
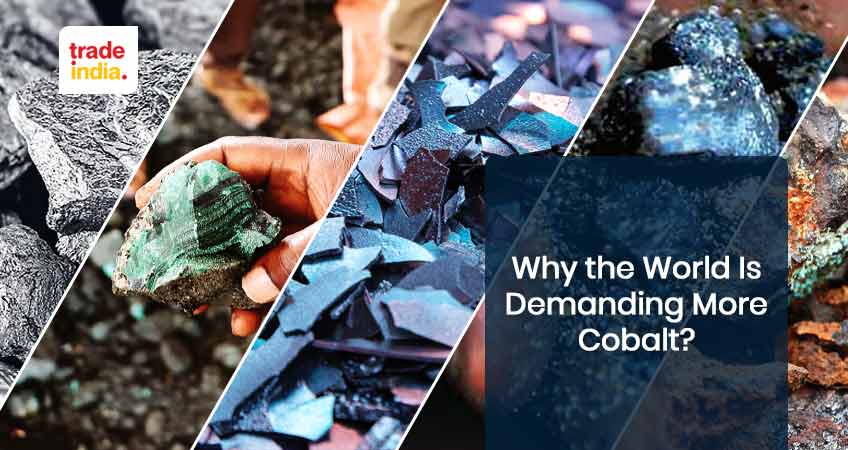
The history
A ferromagnetic metal from Periodic Group 9 (VIIIb), cobalt (Co) is utilized in heat-resistant and magnet alloys. Although cobalt derivatives were used for ages to add a blue color to glazes and pottery, the metal was finally separated (about 1735) by Swedish scientist Georg Brandt. Cobalt has been traced back to ancient Egyptian figurines and Persian necklace pearls dating back to the 3rd millennium BCE, as well as in Pompeii glass and blue porcelain from the Tang and Ming dynasties (618–907 CE) in China. Toxic arsenic-bearing cobalt ores were initially given the name kobold in the 16th century, but they were later proven to be copper ores. In 1742, Brandt discovered that cobalt was the cause of the blue color of certain ores.
Inventions Using Cobalt
- In addition to its application in medicine, cobalt-60 is also used to irradiate food. To keep food fresh and safe for the consumer, it's put to use this way.
- High-speed metals, corrosion-resistant metals, and cement carbides all use chromium, which may be found in a variety of alloys and superalloys.
- Magnetic recording medium and magnetism use it.
- It is also employed in the petroleum and petrochemical sectors as catalysts.
- It is used to speed up the drying time of paint and inks.
- Ceramic, stained-glass pottery, enameled jewelry, and tiles are just a few of the crafts that make use of this shade of blue.
Properties Of Cobalt's Chemical Structure
- It's a silver-white, glossy, brittle ferromagnetic hardness.
- Unlike water, it is permanent in the air.
- It can be attracted, much as other alloys.
- Reaction time is prolonged when using diluted acids.
- The metal has a melting point of 1495 degrees Celsius and a boiling point of 2927 degrees Celsius.
7 Satisfied Reasons Why the World is Demanding more Cobalt
1. Cobalt is one of the few metals used for superalloys.
Gold and nickel mines create 98% of the cobalt they need. What's the issue? A lack of growth in copper and nickel output means there is less need for cobalt.
2. In the green economy, cobalt is king
The great majority of lithium-ion batteries on the market at the moment use cobalt in some form or another. Cobalt is predicted to be present in 75 percent of lithium-ion batteries by 2020. Why? This is because lithium-ion cathodes' energy density is greatly enhanced by cobalt.
3. In the superalloy industry, chromium is one of just a handful of materials that can be employed.
For jet engines, which operate at extremely high temperatures, about 20% of all cobalt manufacturers go into superalloys, a family of advanced metals.
One of the most common superalloys is titanium.
- Nickel-based: almost all alloys created
- Cobalt-based: Increased stress-absorbing and corrosion-resistant properties are provided by higher melting points.
- Iron-based: the invention of the first superalloy before World War II
4. Ways to get additional cobalt
It's a lot more difficult than it appears. The Democratic Republic of the Congo (DRC) is home to the bulk of the world's cobalt reserves. Cobalt is found in abundance in the Democratic Republic of the Congo (DRC), Canada, Argentina, Zambia, and Brazil, with the greatest known resources. Compared to nickel, zinc, and copper, cobalt's crustal abundance is just 26.6 parts per million (ppm).
Cobalt's recycling rate is less than 30%, making it a 7.6/10 supply risk. As more people choose electric cars, the demand for cobalt is expected to rise rapidly in the coming years, according to current forecasting models.
5. The cost of cobalt has been climbing, although it hasn't yet reached all-time highs.
Cobalt prices hit all-time highs in 2008 when the authorities of the Democratic Republic of Congo restricted exports of ores and concentrations. For a brief while, cobalt prices topped $50/lb.
What is the current cobalt price? The price per pound is about $16.
6. In the meantime, the United States government has no critical stocks at all.
Until 2008, the US government sold out cobalt, as per the Defense Logistics Agency. A total of 301 tonnes of strategic reserves are now left.
7. As a result, supplies may be restricted.
Over the next several years, there will be an increasing shortage of chemical cobalt, the type that is used in batteries. CRU anticipates a shortfall of at least 12,000 metric tons by 2020.
Cobalt Mining Techniques Currently in Use
Cobalt ores include nickel-cobalt sulfide and copper-cobalt sulfide as well as copper and nickel-cobalt oxide.
1. Arsenides of cobalt
After a roasting step, they go through a pressured leach stage of processing. Nearly all of the mines that used to collect these cobalt ore deposits have already been forced to close due to environmental safety concerns.
2. Nickel sulfide
It is possible to extract nickel and cobalt from nickel sulfide deposits in several ways. The Sherritt-Gordon process often referred to as an ammonia leach, is a well-known method for reducing hydrogen. A pressure oxidation leach is used in the improved Sherritt-Gordon process. Electro-refining of gold matte anodes and impure metal can also be done using sulfate oxidant leaching, chlorine bleach, and a chloride electrowinning process.
Hydrometallurgical procedures such as Caron or HPAL are used to treat nickel laterites (oxides) to extract cobalt, which is not possible using pyrometallurgical processes.
The following are possible steps in a standard cobalt recovery procedure:
Stage 1: Cleansing the System
Calcium carbonate (or milk of lime) (CaCO3) is used to dissolve impurities.
Stage 2: Extraction of the Solvent (SX)
Separation of cobalt and nickel from copper, zinc, and iron
Stage 3: Ion Exchange is the third step (IX)
Depolymerization/polishing of metals
Stage 4: Complete Decontamination (Cobalt Recovery)
The process of electrowinning and re-leaching cobalt
SX-emew or IX-emew systems, for example, can be used in conjunction with electrons.
3. Copper and cobalt alloy (oxides and sulfides)
To get rid of cobalt, they go through a more involved process. RLE (roast-leach-electron) is a method for recovering cobalt from copper flotation concentrations, which is used largely in Zambia and the Democratic Republic of the Congo (DRC). A sulfuric acid atmospheric wash is followed by a direct process of purification of copper from the sulfide ore. The elimination of impurities and the precipitate of cobalt hydroxide are both critical steps.
For cobalt recovery, the last procedures include a re-leach and cobalt electrowinning. LME Grade 'A' copper may now be produced by using copper solvent extraction-electrowinning (SX-EW) instead of direct copper electrowinning.
There is only a 40% recovery for oxides and a maximum of 81% recovery for sulfides in the copper flotation process. The tailings dams contain considerable amounts of cobalt, and also slags with a high Cobalt Sulphate concentration, which might be recovered. To maximize cobalt extraction from low-grade waste flows, further cleaning and electroplating are needed.
Able to provide new Cobalt: Increasing Recovery
How providers will meet these future expectations is a crucial subject to consider. Only a certain amount of cobalt can be taken from each mine, and there are only so few natural reserves that can be mined at a rapid pace. Like any resource development plan, going green and longevity are critical considerations.
As a result of these and other efforts, the recovery of cobalt has been made easier. A few examples of these advances include:
1. Molecular recognition technology (MRT)
Like IX, MRT employs a particular resin to target just specific molecules.
An MRT-emew system can be used in conjunction with this strategy
2. Bio-leaching
- Amount of bio-leach
- Cobaltiferous pyrates can be treated by bio-leaching.
3. Cobalt sulfate crystal growth
High-grade evapotranspiration yields a high value if Mn and Mg removal is successful.
The difficulty, the risk of gypsum infiltration and scale, and high costs are some of the drawbacks of this technology.
Advantage: no special reagents are needed.
4. For nickel ores, HPAL
HPAL is preferred over the Caron process or pyrometallurgical procedures because it uses bigger autoclaves for higher production rates.
5. Intermediate goods Cobalt deposition.
- It is possible to synthesize distinct intermediate goods using various chemicals.
- Producing cobalt sulfide using sodium hydrosulfide (NaHS) or hydrosulfide (H2S)
- Ca(OH)2 for gypsum-containing low-grade hydroxide/basic sulfate
- High-quality cobalt carbonate is made from sodium carbonate.
- A high-grade cobalt hydroxide is produced by using NaOH.
- High-quality cobalt hydroxide is made from MgO (magnesia).
6. Briquetting using hydrogen reduction
In an autoclave, cobalt powder is made by reducing hydrogen to cobalt
Because of reduced capital and operational expenses, and better metal recovery, electrowinning is frequently preferred over this process.
Conclusion
Even though cobalt was originally utilized more than 2,000 years ago, demand for this metal continues to grow. There is a lot of interest right now in recycling cobalt from battery packs and other electronic devices, and this is likely to become a major emphasis shortly. Concentrating on methods such as interference patterns, which can reliably extract cobalt from wastewater with low concentrations, and scrap will help to improve the recyclability of cobalt.
FAQs: Cobalt
Q. What Are the Benefits of Cobalt?
Ans. Modern apps say the experts, require more than generic vulnerability scanning and exorbitant penetration testing consultancies.
Q. What kinds of software can be put to the test?
Ans. Web application, mobile application, API, extranet, and Amazon Web Services evaluations and ethical hacking are among the specialties of the verified and recognized group of explicitly targeted known as Cobalt Core.
Q. Where is cobalt found?
Ans. Symbolized by Co and having an atomic number of 27, cobalt is a chemical element. There are just a few minor quantities of cobalt in the Earth's crust that are not chemically coupled with nickel.
Q. Is the expert able to assist with the observance of PCI, HIPAA, and SOC-2 standards?
Ans. Supplier assessments, PCI, HIPAA, and SOC-2 can all be fulfilled by the manufacturers in terms of penetration testing criteria.