Why Choose a Centrifugal Pump for Your Business?
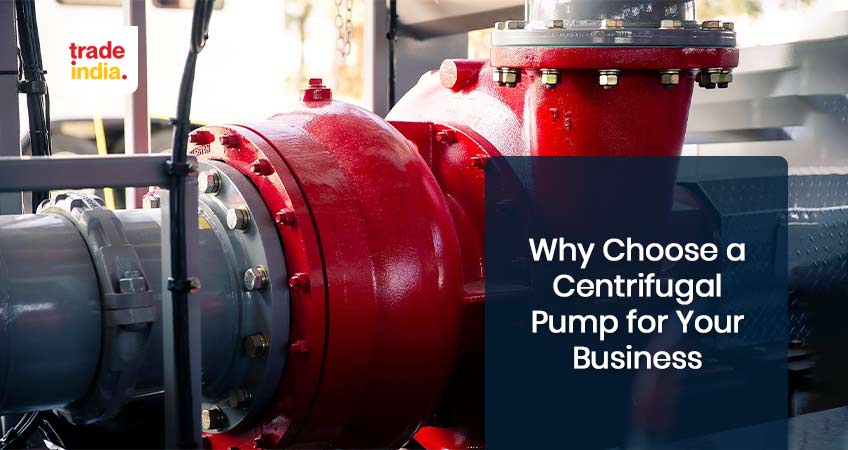
The increasing demands from the agricultural sector have given rise to the centrifugal pump industry as these pumps are used in a wide range of applications. Further information about centrifugal pumps is discussed in this article to get an overview understanding of the industry so that informed decisions can be made to start a centrifugal pump business.
A centrifugal pump is a machine that moves fluid with the transfer of rotational energy. It transfers from one or more impellers or driven rotors. It is along its axis that fluid enters the impeller and is cast out throughout its circumference. The velocity and pressure of the fluid get increased by the impeller while directing it towards the pump exit. The pump casing is designed for compressing the fluid entering the pump and then directing it into the impeller before discharge. The best centrifugal pump manufacturers provide high-quality services and cater to their needs.
The working principle of a centrifugal pump is elaborated as follows:
The impeller of a centrifugal pump is the most important component. It is made up of several curved vanes. Here, an open or semi-open impeller (supported by a single disc) is preferred for fluids containing entrained particles. Liquid enters the impeller at its axis (the 'eye') and escapes between the vanes around the circle. The impeller is attached to a motor through a driving shaft and rotates at a high speed on the opposite side of the eye (typically 500-5000rpm).
The fluid is accelerated out of the impeller vanes and into the pump casing by the impeller's rotational motion. The pump casing is classified into two basic design types namely the diffuser and volute and both of them are used to carry out the same function which is to convert the flow of the liquid into a discharge that is controlled at desirable pressures.
To run a successful centrifugal pump business, it is important to understand the different types of centrifugal pump products, different capacities of horsepower, and most subsequently the end-users that the business will be focusing on and the type of fluid that the pumps will be working with.
Different types of centrifugal pumps
The different types of centrifugal pumps are single-stage pumps, multi-stage pumps, submersible pumps, axial and mixed flow pumps, and circulator and seal-less pumps. Each of them is further discussed in more detail:
1. Single-stage pump
When driven by a motor, a single-stage centrifugal pump makes it possible to comprise one impeller revolving on a shaft to produce fluid flow. It is one of the most basic pump types accessible, with numerous modifications to meet the duty needs of various applications.
2. Multi-stage centrifugal pump
Multistage pumps are those in which the fluid passes through numerous impellers that are connected in series. The type of impeller and circumferential speed plays a big role in the head of a single-stage centrifugal pump. If the rotational speed cannot be raised due to other operating constraints, and a bigger impeller diameter would result in very low specific speeds and inefficient efficiency, connecting many stages in series can be a cost-effective way to increase the head. When the number of stages of a multistage pump is adjusted but the dimensions and speeds remain the same, the flow rate remains constant while the power input and head rise according to the number of stages.
3. Submersible centrifugal pump
A submersible pump is a centrifugal pump that is powered by an electric motor and may function underwater. A series of impellers are spun by a sealed electric motor. Each impeller in the sequence forces water into the eye of the impeller above it via a diffuser.
4. Axial and mixed flow pump
Axial flow pumps are propeller pumps in which the impeller rotates and drives the water forward axially. They are not purely centrifugal pumps. Mixed-flow pumps work partially by centrifugal force and partly by propeller force, with the impeller blades twisted to some degree.
5. Sealless and circulator centrifugal pump
A sealless pump is a centrifugal pump that does not have the dynamic seal that normally seals the pump shaft. To construct a sealed liquid end or pressure boundary, this dynamic seal is replaced by a static containment shell. Circulator pumps in hydronic systems are usually centrifugal pumps that are powered by electricity.
Centrifugal pump capacity
Pump capacity simply means the capacity at which the liquid volume is pumped for a specific period. The capacity of centrifugal pumps is classified into the following three types namely small-capacity pumps, medium-capacity pumps, and large-capacity pumps. Small capacity pumps are commonly used in residential buildings to pump water usually from the ground level to the water tanks on top of the buildings. Medium pumps are commonly used to pump large amounts of liquid usually used in the agricultural sector for irrigation purposes. A large capacity pump is best suited for pumping large amounts of liquid, for example, in the case of emergency scenarios like floods. It is also used in large manufacturing industries where large amounts of fluids are needed to be pumped for manufacturing purposes.
Types of pumps based on end-users
It is important to determine the end-users when planning to start a centrifugal pump business as targeting a wide variety of users will only lead to the business being highly saturated that it does not stand out. The different domains of end-users to consider are industrial users and domestic and agricultural users. The industrial domain of users is further classified into the following sectors namely chemical, wastewater and water treatment, oil and gas, food and beverages, and pharmaceuticals.
Conclusion
In addition to understanding the different types of pumps in the industry, their capacity, user domain, etc. it is advisable to understand the current market scenario of the centrifugal pump industry. You need to make sure to choose superior quality centrifugal pump parts for your requirement. Thorough research is required to be done on the competitors, advantages of centrifugal pump business, restraints, etc. After research has been conducted, registration and other documents will be required to run the business smoothly. Acquiring certifications can also go a long way in making the business appear professional and trustworthy. Financial support may be required to set up a pump manufacturing factory along with experts, staff, technical, and labours to handle the manufacturing process. Raising awareness for the business is also recommended as it can be challenging for a new business to compete with existing companies that have already made a name for themselves in the industry. With a brief overview of the centrifugal pumps, how they work, and the different kinds of centrifugal pumps, one can now confidently start a centrifugal pump business that can thrive in the industry.
FAQs: Centrifugal Pump
Q. What is a centrifugal pump and how does it work?
Ans. A centrifugal pump is a type of pump that converts rotational energy (generally from a motor) into a moving fluid’s energy. It consists of two main parts that play a major role in the conversion of energy:
- Impeller: The impeller part is the rotating part
- Casing: The casing on the other hand is the one that surrounds the first part and is said to be the airtight passage.
Q. What is the difference between a pump and a centrifugal pump?
Ans. The major difference between these two is that a pump will move the fluid required at the same speed without considering the pressure present on the inlet end whereas in the case of a centrifugal pump it is not the same.
Q. What are the advantages of centrifugal pumps?
Ans. The various benefits of a Centrifugal Chemical Pump are highlighted below:
- Corrosion Resistance: These pumps are generally made up of corrosion-resistant materials.
- Energy Efficiency: These are energy-efficient pumps compared to others.
- Smooth Flow: There is always a smooth fluid flow in such types of pumps.
- Proven Reliability: These pumps are highly durable, and one can easily rely on such pumps.
- Low Maintenance: These types of pumps require very less maintenance.
- Size Versatility: These types of pumps are available in different sizes depending on the requirement of the customer
- Application Versatility: These pumps can be applied wherever needed and are easy to handle.
Q. Why do we call centrifugal pumps?
Ans. They are called centrifugal pumps as their working principle is based on centrifugal force. The fluid enters the pumps and obtains energy from the impeller’s centrifugal force which raises its velocity as well as pressure. This pressure then transfers the liquid from place to place.